
BorgWarner installs first Iperion 120 fast chargers
With a single vehicle connected, the Iperion 120 can deliver 120 kW of charging power, or 60 kW per vehicle with two drawing power. Claimed efficiency is 93%.
BorgWarner installs first Iperion 120 fast chargers
In-field analysis, along with a deep knowledge of the power electronics components, enabled BorgWarner Systems to get full power in high ambient temperatures from its new Iperion 120 rapid charger during the initial installation programme in northern Italy, where the first units are in operation (writes Peter Donaldson).
“In the northern part of Italy the altitude is not a problem, but the charger was exposed to very demanding working temperatures,” says charging account manager Davide Spazian. “The challenge to our technical team was to fine-tune the charging station to work in temperatures that can easily reach 40-45 C, and in direct sunlight the internal temperatures can be even higher. Despite that, we needed to guarantee maximum performance in terms of power delivered to the end-user.”
One installation, in Fidenza, was in a high-traffic area near a shopping centre and a restaurant, which brought a high volume of charging during the day. As a result, the charger was “really suffering at first” in direct sunlight, Spazian says.
“The engineering team performed a direct analysis in the field, and were able to work out the right curve for applying the power to achieve the chargers’ full rating,” he adds.
He explains that the team “squeezed the data sheets”, examining the performance capabilities of all the internal components to find “every single degree of operating temperature on each one to be able to set the threshold of each at its maximum,” he says. “We gained 7 C, allowing us to achieve full performance with no degradation of the hardware.”
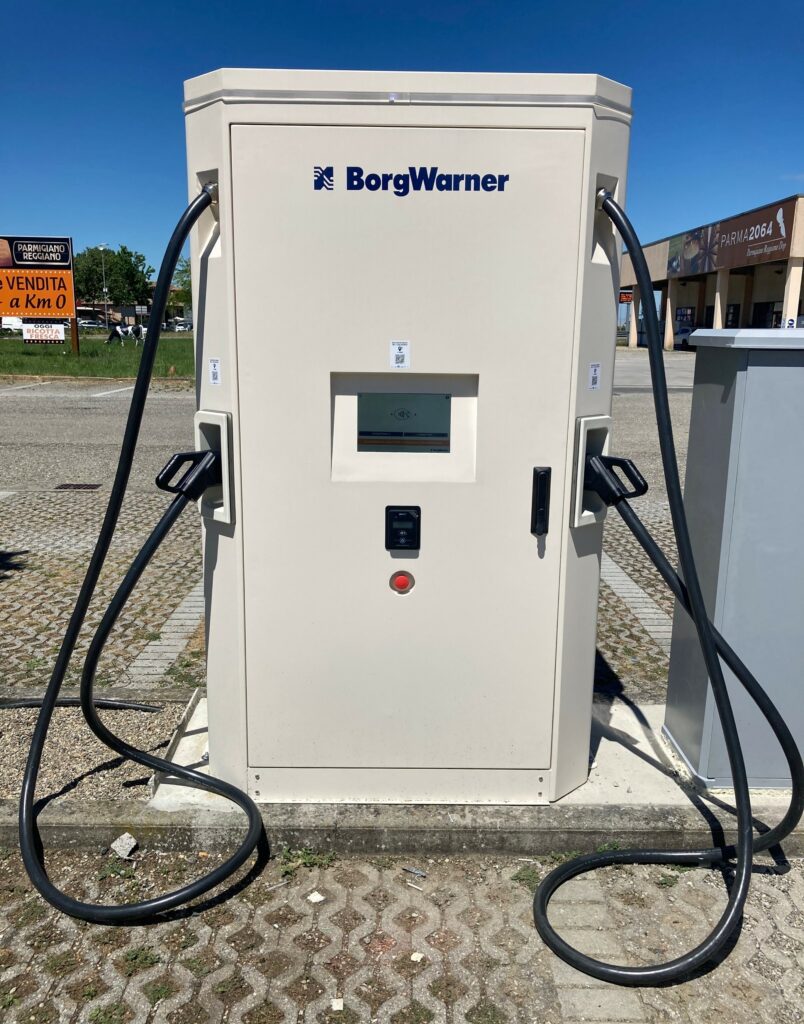
Once the team fully understood the performance limitations of every component, they were able to tune the control software to allow the system to deliver full power without overheating, he adds.
“The key point is that we have full control of the bill of materials and full knowledge of the components installed, because we make 100% of the charger in our facility, and we developed the project entirely in our tech centre,” he says.
“The debug phase and the development and deployment of the solution were compressed into less than a week. That is what it means to be agile in a market that is calling for more performance. As a hardware manufacturer, we have to be very responsive and react quickly to demand, as it allows us to expand more rapidly, which is vital because the time to market is definitely compressed.”
Spazian emphasises that BorgWarner has the goal of taking more than 5% of the total addressable market in Europe by 2027, working with partner companies that install and operate charging stations.
To achieve that ambition, he stresses the importance of securing its supply chain in the face of component shortages. “This is the first challenge we need to face in the long term, and we are already set up to meet that 5% target. We have planned our manufacturing capability and our supply chain accordingly so as not to lose any potential business because of shortages,” he says.